Being able to select a suitable pump for a process is top priority for any process engineer. This guide explains the material selection aspect of pump selection, with a main focus on drinking water processes.
Materials Explained
Most pumps are made primarily out of metal, often stainless steel. The selection process for materials and for pumps in general can vary but normally starts around the time you have defined your other process factors like temperatures, flow rates and pressures.. For this guide, we will assume that you have a fully specified fluid flow (temperatures, desired flow rates, pump power, pressures, etc) and that you only need to select the materials of the pump.
Pump Material Selection Guide
This guide will list all key pump parts for centrifugal and the main types of positive displacement pumps, and any considerations that will need to be done before selecting a material. If this guide is incomplete, let us know in the comments!
Flow Considerations
Some types of conditions are always worth keeping in mind when selecting materials for a pump:
- Seawater and brine: this will speed up corrosion and lead to early pump failure. Commonly, high grade stainless steel is used (e.g. 316).
- High temperature: can impact the longevity of seals and the structural integrity of your casing and impeller, decrease bearing lifetime, and reduce NPSH-available (see this article if you don’t know what that means).
- Varying Speeds and Intermittent Operation: Some pumps only have a small pump curve and operate highly efficiently in a small region, while other pumps have the ability to run at a higher interval along their pump curves without risking stalling or cavitation. Be careful when selecting a pump for a very specific duty when you know that the pump will be varying its load often, or start up and shut down regularly, as this will require additional operational measures such as a priming pump or control valves to avoid damage.
Casing and Axis – all pumps
The pump casing is the key structural component of the pump, and the axis is the load bearing device for the impeller. Very often, these are made of stainless steel. For many pumps, coated stainless steel is more than sufficient but bear in mind that other options such as plastic casings (PVC or similar) exist as well. These plastic alternatives are usually only for low pressure. High pressure will normally always require higher strenght materials, or specialised design if using plastics.
Pump Motor – all pumps
Materials for the pump motors are not normally part of your pump selection, but bear in mind that they should be considered when ambient factors are outside of normal ranges, such as temperatures, pressures, and any chemicals, salt, or spray that may attack the outside of the motor casing.
Impeller – centrifugal pumps only
The impeller is the main pumping element, and therefore bears the brunt of the energy transfer between the pump motor and the fluid. This usually means that a high hardness and corrosion resistance is required, especially for high duty pumps. It is impossible to list all the factors that influence the material choice for your impeller but here are a few:
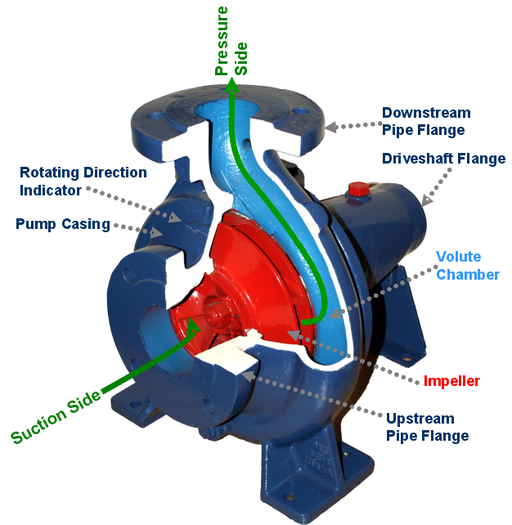
- Temperature: Your fluid must stay within the temperature limit at which the impeller material retains its physical characteristics.
- Corrosion resistance: chemical attack or high salt concentration can cause pitting corrosion on
- Operational range: if your pump runs intermittently and at varying speeds, it is important to consider the additional damage that this can do to your pump. If you regularly run against zero backpressure when starting up, it is key to select a material that can deal with some cavitation as it is highly likely that this will occur.
Seals – all pumps
This is probably the most varied category that is crucial to longevity and safe operation of any pump. Seals are crucial parts that separate compartments, prevent leakage, and in positive displacement pumps ensure that the pistons or other fluid actuators can deliver adequate pressure and flow without leaking but also not wasting energy by friction.
It is key to select seals based on chemical compatibility: even with trace amounts of chemical in wastewater, wrongly chosen seals can wear down in days and cause issues that are difficult to diagnose.
Temperature is another important selection criterion for seals, as they are normally made of elastomers that are sensitive to temperature change. Higher temperatures than the design temp can cause leakage, while low temperatures can cause brittleness and failure under movement.
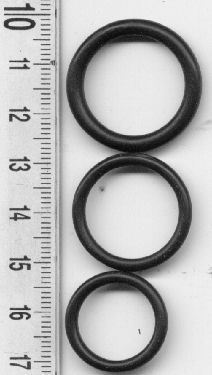